Over the past 30 years, our world has been transformed by the invention of a device that almost everyone on the planet carries with them today. Billions of such devices are produced annually, and by the middle of this century, it is likely to be in the trillions. Of course, that device is the humble lithium-ion battery. As we can imagine, the current technological era is defined by cell phones, which in turn are enabled by semiconductors, radios, and the Internet—a world dominated by cell phones would not have come without the inventions of Goodenough, Whittingham, and Yoshino . In 2019, they won the Nobel Prize in Chemistry for inventing the basic lithium-ion battery in the late 1970s and early 1980s. 1 Since commercialization in 1991, the energy storage capacity of lithium-ion battery technology has increased by a factor of four compared to previous battery technology. As you can imagine, without these improvements, your phone might only last until noon and need a charge, or your phone would become the size of a laptop. Likewise, imagine your laptop with almost all the battery underneath the keyboard, so heavy that you would place it on a desk and never move. Without lithium-ion batteries, we would simply not have the mobile and connected world we have today. In the future, lithium-ion batteries could not only connect billions of people to the Internet, but also in the real world, on land, and in some cases at sea and in the air. Modern electric vehicles have already shown us what is possible, but halving the price (Figure 1), storing 2 times more energy (Figure 2), charging 3 times faster, and extending lifespan by 10 times is all possible and accelerated The transition from fossil fuels to renewable energy. In this article, we discuss the key innovations expected to emerge in the industry over this decade, and their impact on our world.
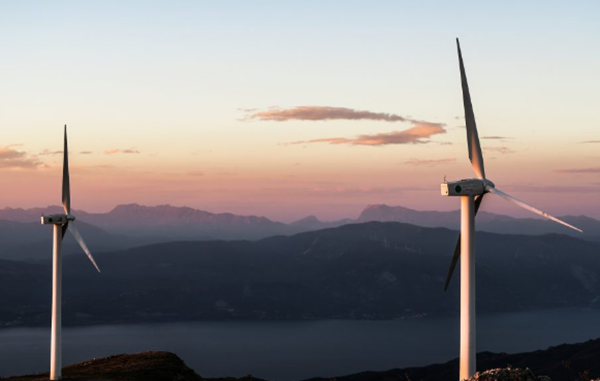
Since Alessandro Volta introduced the first battery about 200 years ago, academia has discovered and tested hundreds of rechargeable battery chemistries, and dozens have been commercially developed in some form (many never fully into production). However, only 4 rechargeable chemistries are commercially significant. Each of these 4 chemical technologies—lead-acid, nickel-cadmium, nickel-metal hydride, and traditional lithium-ion (intercalation type)—requires scientific breakthroughs and significant commercialization efforts. In the future, the fifth chemical technology (advanced lithium ion) still needs more breakthroughs and efforts.
Batteries always require people to make trade-offs. Too often, new technologies that show promise in one performance cause problems in another—leaving most innovations in university labs. The most important innovations should improve multiple performance parameters at the same time, without destroying already excellent performance in other areas.
When lithium-ion technology hits the market, its higher performance makes it the obvious choice over nickel metal hydride. At first, the high cost was not suitable for most applications, but as battery manufacturing scaled up, starting in the late 1990s, lithium-ion batteries experienced a wonderful period of performance improvement and cost reduction. In the mid-2000s, as the most commonly produced 18650 model fell out of favor, the use of more expensive custom pouch cells for each new device became the norm, and cobalt and nickel prices temporarily rose, making lithium-ion battery costs more expensive. The decline gradually slowed down. But costs fell again as EV shipments climbed in 2010, pushing cumulative historical battery production to over 100,000 MWh. Inspired by Swanson’s Law2,3, which tracks and predicts dramatic declines in the cost of solar energy, we have compiled a historical review of data from numerous sources combined with our own industry Changes in costs with scale are forecasted. Despite the increasing rate of capacity growth, the recent flattening of the cost curve suggests that it will take more than just an increase in the production of basic lithium-ion chemistry to continue reducing battery costs and accelerating the adoption of electric vehicles. We need innovation to achieve our goal of 100 million electric vehicles on the road by 2030
Traditional basic lithium-ion batteries function through a so-called “intercalation” mechanism, in which lithium atoms (in ionic form) are inserted (intercalated) into small voids within the crystalline anode material during charging; then move into the crystal during discharging in the small voids within the positive electrode material. 4 No bond cleavage or significant volume change occurs during these processes, so they are almost fully reversible. To borrow an often used analogy, the negative pole is an auditorium into which the lithium ions are seated when the battery is charging – the positive pole is a second auditorium across the hall where the lithium ions go to be seated when the battery is discharged (we’ll use this again not quite Perfect but useful analogy).
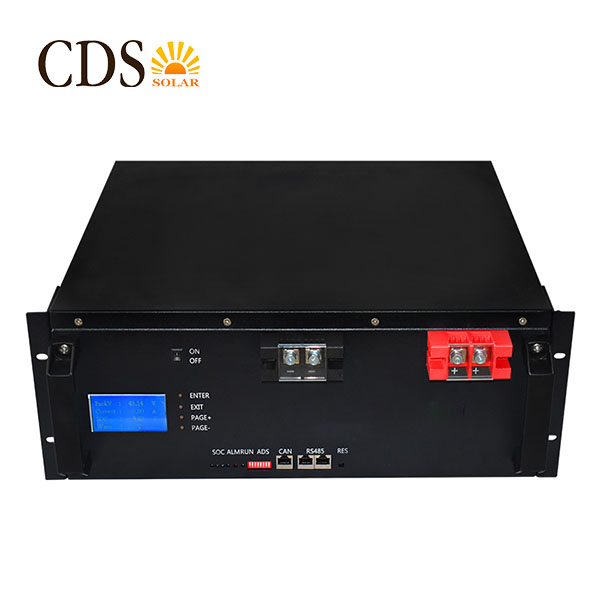
For the negative electrode, only one material is suitable for use in current lithium-ion batteries—graphitic carbon. Several types of graphite account for about 99% of the lithium-ion anode market.
For cathodes, there are two general classes of materials used in automotive lithium-ion batteries, the first of which has several subtypes. They are: (i) higher voltage, higher capacity nickel-rich nickel-cobalt lithium aluminate (NCA) or nickel-cobalt lithium manganese (NCM)5 and (ii) lower voltage, lower capacity lithium iron phosphate LiFePO4 (LFP). 6 Although the cost of nickel and cobalt metals is much higher than that of iron, LFP-based batteries are more expensive than NCA- and NCM-based batteries at the same energy (i.e., in Wh/L) due to the much lower energy density of LFP. Li-ion batteries are 1.3-2 times larger, but NCA and NCM-based batteries are about 25% cheaper (in USD/kWh) than LFP-based batteries. In fact, while each cell made with NCA or NCM is more expensive, resulting in an increase in the numerator “dollar”, these same cells have a higher increase in the denominator energy “kWh”; resulting in a $/kWh energy storage cost lower.
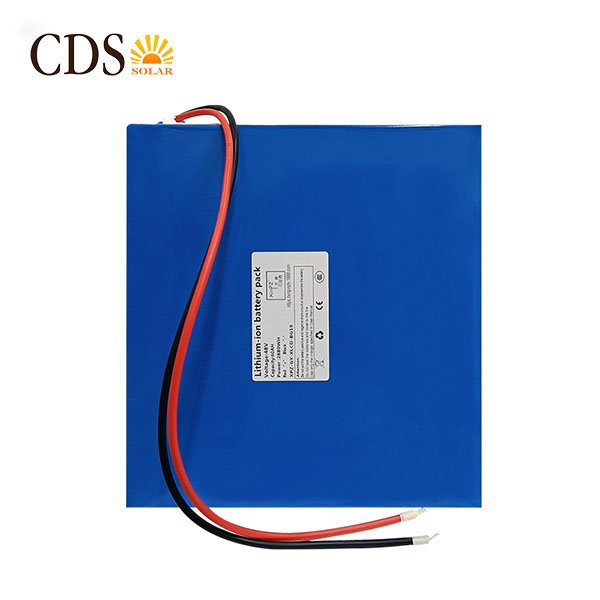
As we mentioned at the beginning of this section, today’s best energy-based batteries have some excellent properties: an energy density of 720 Wh/L and a production cost of about $100/kWh. However, they cannot achieve 5,000 full charge-discharge cycles, and performance degrades after about 1,000 full cycles or equivalently. This means that for an EV with a range of 200-300 miles, performance drops significantly after 20-300,000 miles.
In the automotive sector, these batteries basically use NCA or NCM (usually NCM-622 or more recently NCM-811, where the numbers represent the relative ratios of nickel, cobalt and manganese, i.e. an 8:1:1 ratio of cobalt used 6:2:2 less) positive and graphite negative. At the time of writing, the best of all the energy cells in production appears to be the Panasonic 2170 used by Tesla. In addition to using the highest nickel content (to increase cathode capacity), the cell also incorporates about 5% silicon into the graphite anode to increase anode capacity. In addition to creating the highest energy density battery at 720 Wh/L, it also proved to be the cheapest. The reason is simple – we measure cost in terms of unit price per kWh, so even if the cost of the battery itself remains relatively flat, as battery storage increases (kWh), the price per kWh decreases. The more energy you put into the battery, the lower the unit price per kWh. However, energy-based battery designs can degrade battery cycle life and charge rates for several reasons that we describe next.
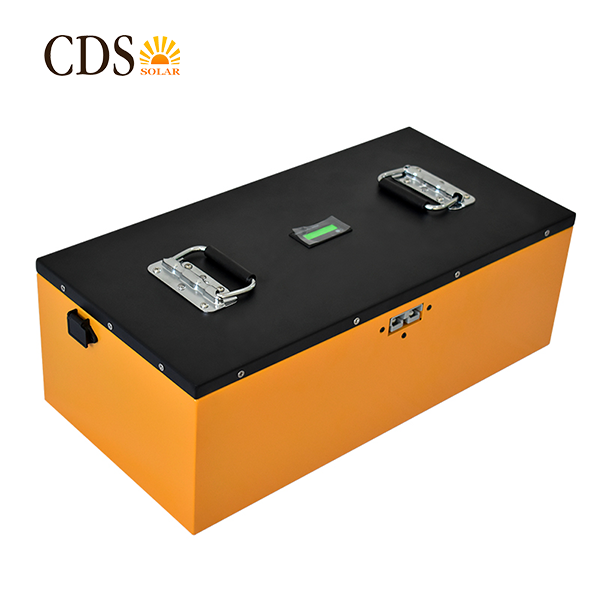
Today’s best power-type batteries can achieve the other best-in-class features we covered in the beginning: 5,000 charge-discharge cycles and a 10-minute full charge. But these cells cannot achieve the same cost as energy-based batteries – 25-50% higher on a per-kWh price basis – and only have an energy density of 450 Wh/L, compared to 720 Wh/L for energy-based batteries It pales in comparison. A further auditorium analogy can be used to explain the combination of the advantages of fast charging of power batteries with the disadvantages of low energy density. Imagine a LFP but only one third of the seats installed compared to the NCA and NCM auditoriums. All other seats have been removed, leaving an aisle between each chair. So it’s easier for all the people entering the auditorium (lithium ion) to run to their seats without much hindrance. Despite the disadvantages of high cost per kWh and low energy density, power batteries have been a very popular choice in the electric vehicle industry in China, and there are even rumors that Tesla will launch it in the Chinese market in 2021. The product. In many cases it can also be the best choice for grid applications.
The theoretical limit of battery performance is always limited by key components – anode, cathode, electrolyte and separator. The actual achievement of these performance goals is limited by manufacturing excellence. This section presents expected innovations in lithium-ion battery components. We describe the manufacturing innovations that assemble these components in the next section.