The wind resistance of photovoltaic power generation equipment has a direct impact on its safety, service life, and manufacturing costs. Currently, the photovoltaic device with the highest power generation efficiency is a two-dimensional tracking photovoltaic power generation device. The device always tracks the sun’s azimuth and elevation movements, ensuring that the photovoltaic panel is perpendicular to the direction of illumination to the maximum extent. Tracking photovoltaic power generation devices are more complex than fixed structures, and as photovoltaic panels track the rotation of the sun, the wind load they are subjected to is constantly changing. The main research work of this paper is as follows:
(1) Using the finite element method for fluid-structure coupling simulation, wind load simulation of tracking photovoltaic power generation equipment with different attitude angles is conducted. The variation law of wind load with attitude angle is studied, and the reason why the maximum wind load occurs at a specific attitude angle is analyzed.
(2) The correctness of the above simulation methods and conclusions is verified by collecting experimental data through the wind torque measurement experimental system and comparing the measured and simulated values.
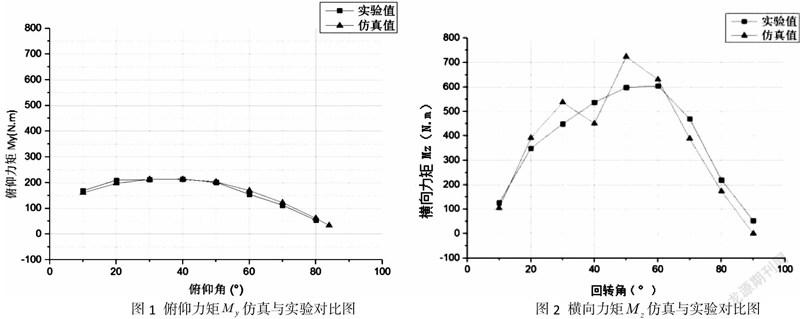
1.Research background
The dual axis tracking photovoltaic power generation equipment is the research object of this article. It has two rotating axes that rotate to track the orientation and elevation of the sun, maintaining that the photovoltaic panel always tracks the motion of the sun, and improving the power generation efficiency by about 35% compared to the fixed type. Its maximum daily wind speed is 14m/s, and its maximum wind resistance wind speed is 28m/s.
Tracking photovoltaic power generation equipment has a special working environment and solar tracking structure. Since the photovoltaic panels of the equipment always track the sun’s motion, the wind load is the most complex. This article adopts the method of computational fluid dynamics, which is based on fluid mechanics and uses numerical calculation as a tool to analyze flow problems.
Currently, there are some problems with tracking photovoltaic power generation equipment: the drive torque of the reducer is too small, and the design torque does not match the actual working torque. In windy weather, the speed reducer is often overloaded, requiring regular maintenance of the speed reducer;
The research purpose of this article is to solve the practical engineering problem that the speed reducer of tracking photovoltaic power generation equipment is prone to overload, which has engineering guiding significance for the development and design of this equipment.
2.Definition of wind force and wind moment
The forces exerted by wind loads on objects can generally be simplified into wind force and wind moment, and can be simplified into three forces and three moments according to the coordinate system. Referring to the antenna structure wind body axis coordinate system [1], this paper establishes a body axis coordinate system based on the axis of the solar retarder. For the wind force in three-dimensional space, the directions of the wind force in space are usually represented by the,, and three axes, respectively. The six components of the volumetric coordinate system are:
Axial force, along the axis of the equipment;
Lateral force, along the axis of the equipment;
Lateral force, perpendicular to the ground in the direction of the pitch axis;
Rolling moment, the moment axis is consistent with the axis;
Pitch moment, the axis of the moment is consistent with the axis and coaxial with the rotation axis of the pitch reducer;
Lateral torque, the axis of the torque is consistent with the axis and coaxial with the rotating shaft of the rotary reducer;
Axial force, lateral force, and lateral force can be combined into wind resultant force.
3.Wind load simulation modeling of photovoltaic panels
According to the geometric parameters of tracking photovoltaic power generation equipment, a geometric model and a fluid domain are established. The model in this paper is composed of two 8.0m long models × 1.9m × For a 0.04m flat plate, determine the size of the fluid domain as: 70 m × 55 m × 25 m, the height from the center of the model to the ground is 4.2 m, and the distance from the entrance surface of the wind to the center of the model is 20 m; The simulation model is divided into appropriate grids, which are more dense at locations where the flow velocity changes greatly, improving the calculation accuracy; According to the actual fluid wind environment, a standard turbulence model is set and selected. The material of the fluid domain is air. The normal inlet wind speed is set to be 14 m/s, the temperature is 20 ℃, and it is adiabatic. The reference pressure is 1 standard atmospheric pressure. The fluid is considered as an incompressible fluid; According to the characteristics of the simulation model, a fluid structure coupling solver is selected; Finally, the wind force and wind torque of various attitude angles are obtained through post processing calculations.
4.Wind load analysis of photovoltaic panels with various attitude angles
Because photovoltaic panels always track the sun’s rotation, their upwind angle is constantly changing. After simulation, the wind loads of photovoltaic panels with various attitude angles are calculated. This section studies the variation of wind load with attitude angle, the maximum value, and the reasons for the maximum value at a specific angle.
According to the simulated wind force and wind torque of photovoltaic panels with various attitude angles, the influencing factors and variation trends of wind load are studied; Based on fluid simulation, the cause of the maximum wind load generated by a specific attitude angle is studied. The main conclusions are as follows:
(1) Anisotropic wind force is mainly related to the upwind projected area of the force direction. The reason for the formation of wind force is the pressure difference resistance on the surface of the photovoltaic panel. The upwind surface of the photovoltaic panel blocks the passage of fluid to form a positive wind pressure, and the wake area of the leeward surface forms a negative wind pressure;
(2) The wind torque in each direction is mainly related to the windward area and the eccentric wind load force at a specific angle. The wind torque is caused by the eccentric wind force and edge vortex suction generated by the uneven wind pressure on the surface of the photovoltaic panel;
(3) When the rotation angle is 0 ° and the pitch angle is 90 °, the windward area is the largest, and the wind resultant force is the largest. The maximum value is 5572N, which is the maximum wind load force of the photovoltaic panel;
(4) When the rotation angle is 0 ° and the pitch angle is 30 °, the uneven wind pressure on the photovoltaic panel generates a torque in the y-axis direction. The maximum pitch torque is 1649.2N · m, which is the wind load torque of the pitch reducer;
(5) When the rotation angle is 60 ° and the pitch angle is 90 °, the uneven wind pressure on the photovoltaic panel generates a torque in the z-axis direction, with the maximum lateral torque of 5084.4N · m. This value is the wind load torque of the rotary reducer.
5.Experimental verification of wind load simulation calculation for photovoltaic panels
The wind load simulation calculation results are verified by measuring the wind load through experiments. This paper conducts experiments in a natural low wind speed environment: Firstly, collect low wind speed environmental parameters at the experimental site and conduct wind load simulation; Then, experimentally measure the load torque of the solar speed reducer; Finally, the correlation between simulated and measured wind moments is compared to verify the correctness of low wind speed wind load simulation and the feasibility of the fluid structure coupling simulation method.
1) Compare the simulated and measured values of the pitch torque
As shown in Figure 1, the data are analyzed: the average value of the experimental values is 165.7 N · m, the minimum value is 53.8 N · m, and the maximum value is 214.1 N · m; The average value of the simulation value is 167.3 N · m, the minimum value is 33.5 N · m, and the maximum value is 213 N · m; The Pearson correlation coefficient between the simulated value and the measured value is 0.87, showing a high linear correlation.
2) Compare the simulated and measured values of lateral torque
As shown in Figure 2, the data in the table are analyzed: the average value of the experimental values is 378.5N · m, the minimum value is 53.2N · m, and the maximum value is 604.7N · m; The average value of the simulation value is 377.9 N · m, the minimum value is 0.4 N · m, and the maximum value is 724.4 N · m; The Pearson correlation coefficient between the simulated value and the measured value is 0.85, showing a high linear correlation.
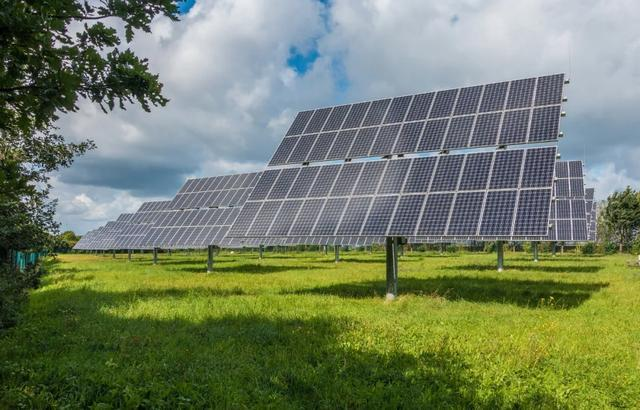
6.Conclusion
This paper studies the wind load composition, theoretical calculation methods of wind load, and wind flow characteristics of photovoltaic panels, providing a theoretical basis for analyzing wind load. A wind load model was established, and the wind load simulation analysis of tracking photovoltaic power generation equipment with different attitude angles was carried out using the fluid-structure coupling simulation method. By analyzing simulation data, the law of wind load changing with attitude angle is studied. Based on the flow field and wind pressure simulation diagram, the reason for the maximum wind load at a specific angle is analyzed. On existing equipment, a set of wind torque measurement experimental system has been installed to compare and analyze the measured and simulated wind torque values, verifying the credibility of the simulation method.
In this study, using the fluid solid coupling module of COMSOL Multiphysics software, the wind load on photovoltaic panels was simulated, and the distribution characteristics of actual wind pressure were simulated. The reliability and feasibility of the simulation modeling method were basically confirmed through experiments. The wind load simulation method in this paper has engineering guiding significance for the development and design of photovoltaic equipment.